The most common materials used in piping industries are various grades of steel. Hebei Haihao Group produce the piping poducts in steel materials of these grades, follows are some materials we used :
1. Carbon Steel .
Carbon steel is the most common steel materials used in the piping industry, carbon steel pipe fittings are used in general refinery factories, chemical industry and process plants . They are also used in neutral or aqueous solutions services. Carbon steel has a working temperature from -29℃ to 427 ℃ commonly. The carbon steel materials also have the high strength carbon steels and low temperature carbon steels (LTCS) , the low temperature carbon steels could be used in the temperature of – 46℃.
There is one kind of the good quality carbon steel, killed carbon steel , they are thoroughly deoxidized when melting them.The killed carbon steel materials is clearner and better quality than common carbon steels, they have fewer air bubbles.
2. Low Alloy Steel.
Alloy steel materials means the steel elements contain one or more alloying , such steels can improve the mechnical strength,temperature characters or corrosion resisting properties than carbon steels. For example, Cr element and Si element can improve the hardness ,abrasion resisting and corrosion resisting. Ni element can improve the toughness and low temperature properties and corrosion resistance. Mo element can make sure the high strength in a high temperature,commonly the alloy steel materials are used from -29℃ to 593℃. Here are some regular alloy steel materials:
0.5% Mo : These low alloy steels are used for higher temperature services and most frequently for intermediate temperatures for its resistance to hydrogen attack. They have the same maximum temperature limitation as killed steel (ASME Code 1000 deg. F) but the strength above 700 deg.F is substantially greater.
0.5% Cr 0.5% Mo and 1.25% Cr 0.5% Mo: These alloys are used for higher reistance to hydrogen attack and sulphur corrosion. They are also used for services where temperatures are above the rated temperature for 0.5% Mo steel.
2.25% Cr 1% Mo and 3% Cr 1% Mo: These alloys have the same uses as 1.25% Cr, but have greater resistance to hydrogen attack and higher strength at elevated temperature.
5% Cr 0.5% Mo: This alloy is used most frequently for protection against combined sulphur attack at temperatures above 550 deg.F. Its resistance to hydrogen attack is better than 2.25% Cr,1% Mo.
9% Cr 1% Mo: This alloy is generally limited to heater tubes. It has a higher reistance to high sulphur stocks at elevated temperatures. It also has a maximum allowable metal temperature in oxidising atmospheres.
0.5% Cr 0.5% Mo and 1.25% Cr 0.5% Mo: These alloys are used for higher reistance to hydrogen attack and sulphur corrosion. They are also used for services where temperatures are above the rated temperature for 0.5% Mo steel.
2.25% Cr 1% Mo and 3% Cr 1% Mo: These alloys have the same uses as 1.25% Cr, but have greater resistance to hydrogen attack and higher strength at elevated temperature.
5% Cr 0.5% Mo: This alloy is used most frequently for protection against combined sulphur attack at temperatures above 550 deg.F. Its resistance to hydrogen attack is better than 2.25% Cr,1% Mo.
9% Cr 1% Mo: This alloy is generally limited to heater tubes. It has a higher reistance to high sulphur stocks at elevated temperatures. It also has a maximum allowable metal temperature in oxidising atmospheres.
3.Stainless Steel :
Besides carbon steel and alloy steel,the stainless steels also are regular piping materials. They are corrosion resistant ,works in high temperature and easily fabricated into complex shapes,commonly they works in temperature from -257 ℃ to 538℃. There are 3 kinds of Stainless steels:
Martensitic stainless steel : Martensitic alloys contain 12-20% Cr with controlled amount of carbon and other additives. Type 410 is typical material of this. They can be hardened by heat treatment, which can increase tensile strength. Corrosion resistance is inferior to Austenitc Stainless steels and these are generally used in mild corrosive environments.
Ferritic stainless steel: Ferritic steels contain 15-30% Cr with low carbon content( 0.1%). Because of the higher Cr content ,it improves corrosion resistance. A typical Ferritic stainless steel is Type 430. The strength of these can be increased by cold working but not by heat treatment. Type 430 is widely used in nitric acid plants. In addition, it is very resistant to scaling and high temp oxidation upto 800 ℃.
Austenitic stainless steel: Austenitic steels are the most corrosion resistant of the three groups. These steels contain 16-26% Cr 6-22% Ni. Carbon content is low(0.08% max) to minimize carbide precipitation. Welding may cause Cr carbide precipitation, which deplete the alloy of some chromium and lowers its corrosion resistance in some specific environments, notably nitric acid. The carbide precipitation can be eliminated by heat treatment(solution annealing). To avoid precipitation special steels stabilized with titanium, niobium, or tantalum have been developed(Types 321,347 & 348). Another approach to the problem is the use of low carbon stainless steel such as types 304L & 316L with 03% max carbon.
The detailed list of common steel materials in piping industries are as follows:
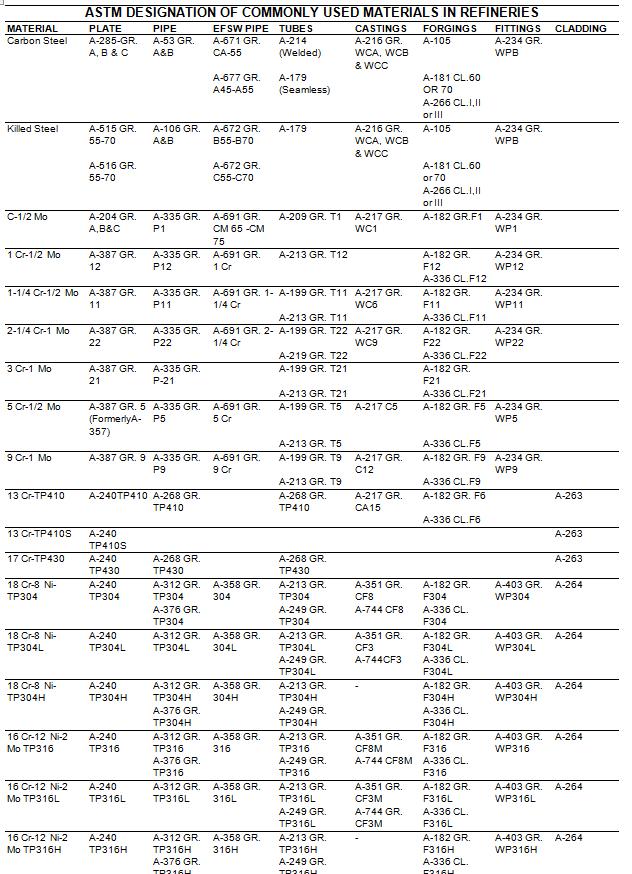
Steel-Piping-Materials-list
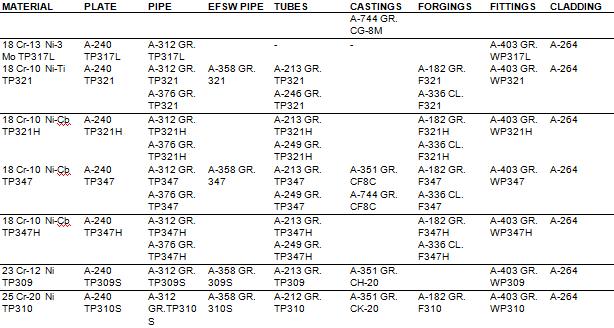
Steel-Piping-Materials-list2